- Details
- Geschreven door Paul Denneman Paul Denneman
Artikelindex
Als de voorraad van een productiebedrijf in geld wordt uitgedrukt, vertegenwoordigt deze een aanzienlijk bedrag. Bepalen we de waarde van de voorraad ten opzichte van het totale balans, dan zien we vaak ratio's van 30% of meer.
Een vuistregel is dat de voorraadbeheerskosten gemiddeld 20-25% van de balanswaarde van de voorraad omvatten. Het is dan niet moeilijk te begrijpen dat er aanzienlijke bedragen zouden kunnen vrijkomen wanneer we erin slagen de voorraden te reduceren. Dit vrijkomende geld kan dan weer worden ingezet voor andere investeringen.
Daarnaast maskeren hoge voorraden vaak andere problemen binnen het bedrijf: er is een slechte afstemming tussen vraag en aanbod, er zijn kwaliteitsproblemen, de productietijden zijn te lang, enzovoort. In een situatie met minimale voorraden zal de schade in het geval van kwaliteitsproblemen minder omvangrijk zijn. Er zijn immers minder producten bij betrokken. En wat als, zoals het geval bij de kredietcrises, de vraag ineens met 20 tot 40% terugvalt? Ons vermogen zit dan vast in moeilijk verkoopbare goederen.
En zelfs als onze onderneming gestroomlijnd is, dan nog houden voorraden een risico in: incourantheid, schade, bederven, enzovoort. Kosten die verborgen zitten in de balanswaarde van de onderneming.
Figuur 1. Het model van de rivier en de stenen
In het laatste decennium is er een kentering gekomen in de houding tegenover het fenomeen 'voorraad'. Nog niet zo lang geleden lazen we in elk boek over dit onderwerp een pleidooi voor het belang van het aanleggen van voorraden uit veiligheidsoverwegingen of als buffer (de Just in Case-filosofie). Mede onder invloed van de Japanse productiefilosofie zijn we heel anders tegen deze problematiek aan gaan kijken. Vandaag de dag worden voorraden gezien als de bron van alle kwaad en moeten als zodanig tot het absolute minimum beperkt worden (de Just in Time-filosofie). Hierbij verplaatsen voorraden zich naar de toeleveranciers in de logistieke keten.
Definitie voorraad
Een simplistische definitie voor voorraad is: 'goederen die je in bewaring houdt voor later gebruik'. Beschouwen we dit meer in detail, dan ontdekken we dat er in principe vier soorten voorraden bestaan.
- Grondstoffen
Alle materialen die nodig zijn als input in het productieproces. - Goederen in bewerking (work in progress)
Gedeeltelijk afgewerkte goederen die deel uitmaken van de goederenstroom tijdens het productieproces. - Eindproducten
Outputs van het productieproces, terug te vinden binnen de logistieke keten. - Hulpstoffen
Goederen die in een organisatie verbruikt worden, maar niet direct in het eindproduct terug te vinden zijn. Dit zijn bijvoorbeeld voorraden van emballage, verpakkingsmaterialen, kantoorartikelen en reserveonderdelen.
De laatste categorie goederen noemen we ook wel MRO-artikelen, wat staat voor maintenance, repair and operating-artikelen. Deze goederen zijn noodzakelijk voor het functioneren van de organisatie in het algemeen en voor het herstel en onderhoud van productiemiddelen in de indirecte sfeer in het bijzonder. Een categorie die vaak in de marge wordt meegenomen, maar veelal een hoge waarde vertegenwoordigt en niet op de balans wordt opgenomen. Bij het niet op het juiste moment beschikbaar zijn van de goederen kunnen die tot aanzienlijke (stilstands)kosten leiden.
Redenen voor voorraad
Er zijn vier factoren die het aanhouden van voorraden rechtvaardigen.
Tijd
Er verloopt een zekere tijdspanne tussen het bestellen van de grondstoffen en het effectief aanwenden ervan in het productieproces. Dit is analoog aan het tijdsverschil dat bestaat tussen de productie en de verkoop van de afgewerkte producten. De voorraden die worden opgebouwd, vervullen dus een bufferfunctie, als schokdemper tussen de verschillende ritmes van de leveranciers, de eigen productie en de klanten. Het eventueel inkorten van die tijdspanne zal dus de voorraad drukken. Een ander voorbeeld van de categorie 'tijd' is de voorraad die ontstaat doordat goederen onderweg zijn. We kunnen hierbij denken aan goederen die in China worden geproduceerd en onderweg in de container zitten. Deze voorraad kan ook als tijdsbuffer worden gezien.
Onzekerheid
In een dynamische omgeving loopt niet alles zoals we het zouden wensen. De vraag van de klant is onzeker en kan variëren ten gevolge van diverse factoren. Door het uitvallen van machines kunnen leveringstermijnen wijzigen. Ook kan de onzekerheid toenemen door een staking van het personeel of kwaliteitsproblemen. Het aanvaarden van en het anticiperen op deze onzekerheid zal dus aanleiding geven tot meer voorraad. De grote uitdaging bestaat er echter in om de oorzaken van die onzekerheid weg te nemen. Enkele voorbeelden hiervan zijn de moeite die we ons getroosten op het vlak van totale kwaliteitszorg, het verbeteren van de relaties met leveranciers en de inspanningen om het productieproces beter onder controle te krijgen.
Economisch motief
Door de aanwezigheid van voorraden kunnen we het personeelsbestand relatief stabiel te houden. Dit geldt in het bijzonder voor producten die onderhevig zijn aan seizoensschommelingen. Bedrijven houden ook voorraden aan ter anticipatie op prijsstijgingen en wisselkoersschommelingen. De bepaling van de ordergrootte zelf is een afweging van voorraad versus het aantal om- of bestellingen.
Aanbod van goederen
Anderzijds kan voorraad ontstaan door beperkingen aan de aanbodzijde. Zo zal een groenteconservenfabriek afhankelijk zijn van het aanbod van groenten en zal daar de productie op afstemmen. De gecreëerde voorraad zal vervolgens verkocht gaan worden. Bij een aanbodstructuur kijken we meer naar de mogelijkheden van onze leveranciers.
Vraag en aanbod bepalen de voorraad
De klantvraag is over het algemeen grillig en onzeker. Om deze variaties op te vangen is het aanhouden van voorraden meestal de door de markt gewenste oplossing. Voor het bepalen van de hoogte van de voorraden gaan we over het algemeen uit van de vraagstructuur. Bij de vraagstructuur onderscheiden we de onafhankelijke vraag en de afhankelijke vraag. De onafhankelijke vraag is de marktvraag naar eindproducten, terwijl de afhankelijke vraag de vraag naar componenten (subassemblages) en vaak ook de vraag naar reserveonderdelen weergeeft. Dit brengt met zich mee dat de eerste niet op een deterministische wijze kan worden bepaald. Er bestaan wel enkele technieken om deze zo nauwkeurig mogelijk te voorspellen, waarbij rekening kan worden gehouden met seizoenschommelingen of trendbewegingen. Een voorbeeld van een dergelijke techniek is de moving average-methode. Van periode tot periode kan de vraag constant of variabel zijn. Wanneer de omvang van de vraag op voorhand gekend is, spreken we van een deterministisch systeem. Is dit niet zo, dan heeft men een stochastisch systeem, waarbij de vraag een bepaalde verdelingsfunctie volgt die zowel discreet als continu kan zijn.
Afhankelijk van het voorraadmodel kan de lotgrootte constant of variabel zijn. Hetzelfde geldt voor de tijd tussen twee bestellingen of productieruns. Er kunnen tevens enkele seizoensgebonden elementen meespelen (bijvoorbeeld agrarische productie). In het geval van eigen productie moet rekening worden gehouden met de productiesnelheid, de wachttijd tussen verschillende machines, transporttijden, enzovoort. Daarnaast kunnen er verschillende beperkingen aanwezig zijn. We kunnen hierbij denken aan een maximale productiecapaciteit (het aantal machine- of manuren), een beperking in het aantal omstellingen of bestellingen, er kunnen financiële beperkingen zijn of ruimtelijke restricties, beperkte houdbaarheid of levensduur van producten, enzovoort. Met al deze aspecten moeten we rekening houden wanneer we spreken over een efficiënt voorraad- en productiebeleid.
Beheersing van de voorraad
Als we spreken over voorraadsystemen, waar hebben we het dan eigenlijk over? Bedoelen we de wijze waarop we de voorraad fysiek gesproken bewaren of bedoelen we de methoden waarmee we de voorraad uiteindelijk trachten te beheersen? Bij de wijze waarop we de voorraad fysiek bewaren, spreken we meestal niet over 'voorraadsystemen', maar over 'opslagsystemen'. De systemen waarmee we de voorraad trachten te beheersen, bepalen 'het systeem van beheersing van de voorraad'.
Onder een voorraadsysteem verstaan we de wijze waarop er binnen een organisatie beslissingen worden genomen ten aanzien van:
- het al dan niet aanhouden van voorraad;
- de hoogte van de aanwezige voorraad;
- het tijdstip van aanvullen van de aanwezige voorraad.
Deze beslissingen tezamen worden ook wel 'voorraadbeheersing' genoemd.
Bekijken we de evolutie van voorraadsystemen, dan zien we de volgende belangrijke stromingen:
- Vanaf 1950: klassieke voorraadtheorie --> Statistical Inventory Control (SIC)
- Vanaf 1970: productketenbenadering --> Material Requirements Planning (MRP)
- Vanaf 1980: nulvoorraadbenadering --> Just in Time (JIT)
- Vanaf 1985: knelpuntbenadering --> Theory of Constraints (TOC)
- Vanaf 1995: ondernemingsbenadering --> Enterprise Resource Planning (ERP)
- Vanaf 2000 Ketenbeheersing --> Supply Chain Management (SCM)
Binnen een onderneming kunnen verschillende voorraadsystemen naast elkaar bestaan. Zo zal de voorraad kantoorartikelen bij veel bedrijven op een andere wijze worden beheerd dan de voorraad grondstoffen. Bij de keuze van een voorraadbeheersingssysteem is het in de eerste plaats van belang te identificeren welke verschillende soorten voorraad er binnen de onderneming aanwezig zijn. Daarnaast moet de tijd die wordt gestopt in de beheersing van de voorraad in verhouding staan tot de waarde van de voorraad en de kosten die 'nee-verkoop' met zich meebrengt.
Klassieke voorraadtheorie
Ook al lijkt de klassieke voorraadtheorie door het verstrijken van de tijd achterhaald te zijn, toch komen er nog vele elementen terug in de hedendaagse praktijk van het voorraaddenken. De klassieke voorraadtheorie gaat ervan uit dat we de optimale voorraadhoogte en het optimale bestelinterval kunnen afleiden uit een aantal parameters.
Voor het gemak gaan we ervan uit dat we zekerheid hebben ten aanzien van een veelheid van factoren die een rol spelen in de onderliggende modellen. Dus wanneer de gevraagde hoeveelheid bekend is, alle kosten constant zijn en wanneer de leveranciers stipt op tijd de gevraagde hoeveelheid leveren, kan ervoor worden gezorgd dat er precies voldoende artikelen in voorraad zijn. In dat geval is er keuze tussen frequente leveringen van kleinere hoeveelheden en minder frequente leveringen van grotere hoeveelheden. In de gedachtegang van de klassieke voorraadtheorie is voorraadbeheersing het bepalen van twee parameters, te weten:
- bestelinterval;
- bestelhoeveelheid.
Dit geeft vier elementaire voorraadsystemen (zie figuur 2).
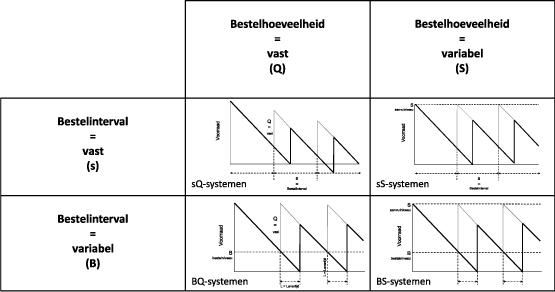
Figuur 2. Voorraadaanvulsystemen
Voor de bepaling van de optimale bestelhoeveelheid kunnen we gebruikmaken van de bekende 'formule van Camp'. Voor de bepaling van het optimale bestelinterval zijn vele formules beschikbaar. In het kader van dit artikel zou het te ver voeren om hier uitgebreid op in te gaan.
Voorbeeld eenvoudig voorraadbeheer
U rijdt auto en die heeft van tijd tot tijd brandstof nodig. Nu zijn er verschillende manieren om ervoor te zorgen dat uw tank afdoende gevuld blijft.
U stelt bijvoorbeeld uw dagteller na iedere tankbeurt op nul. Bereikt de teller een bepaalde waarde, dan gaat u naar de tank. Ook kunt u blindvaren op het brandstoflampje. Gaat deze aan, dan rijd u naar de eerste tankmogelijkheid en vult u de tank. Dit zijn beide uitvoeringsvormen van een systeem met een variabel bestelinterval. Maar u kunt ook van regelmaat houden. U rijdt bijvoorbeeld iedere zaterdag naar het tankstation en vult uw tank bij. Dit laatste is een voorbeeld van een vast bestelinterval.
Eenmaal bij het tankstation aangekomen moet een besluit worden genomen over de hoeveelheid brandstof. U moet als het ware uw bestelhoeveelheid bepalen. Tankt u helemaal vol (variabele bestelhoeveelheid), tankt u iedere keer voor € 50,– of is uw ritme iedere keer 30 liter (een vaste bestelhoeveelheid).
Het mag evident zijn dat de methode die u kiest, afhankelijk is van uw rijgedrag (vraagpatroon). Is uw vraagpatroon erg wisselvallig, dan zult u met gebruik van het verkeerde systeem een groter risico van een lege tank lopen. Gelukkig zijn daar ook remedies voor. U kunt een veiligheidsvoorraad aanleggen door een reservetankje achter in de auto te leggen. Het moment dat uw brandstoflampje aangaat, is ook niet geheel willekeurig gekozen. Dit gaat branden op het moment dat u redelijkerwijs nog een tankstation kunt tegenkomen om uw tank bij te vullen. In Nederland liggen de tankstations dicht bij elkaar, zodat deze voorraad redelijk hoog is. Maar dat is, zoals u misschien al eens aan den lijve ondervonden hebt, niet in alle Europese landen het geval.
Als we net als in de jaren zeventig de benzine weer op de bon zouden zetten, gaan we over van een vraag- naar een aanbodsysteem. In een dergelijk systeem moeten we de 'tering meer naar de nering zetten'. Ook in dat systeem kunnen de voorraadaanvulmodellen worden toegepast. Maar dan kan het bestelinterval en/of de bestelhoeveelheid in sterke mate worden beperkt door de regulering van het aanbod.
De hiervoor genoemde modellen zijn zogenoemde 'deterministische modellen' en houden dus geen rekening met allerlei fluctuaties in het vraagpatroon en de levertijden. Om die reden zijn er uitbreidingen op deze modellen gemaakt waarbij een veiligheidsvoorraad en servicegraad bepaald worden. Deze uitbreidingen worden 'stochastische voorraadmodellen' genoemd. Het zijn dan ook deze modellen waardoor het toepassen van het klassieke voorraaddenken ook wel Statistical Inventory Control (SIC) wordt genoemd.
De nadelen van beide zienswijzen uit de klassieke voorraadtheorie zijn:
- Er wordt slechts een optimum van de logistieke kosten bepaald voor één schakel in de logistieke keten.
- Alle artikelen worden behandeld alsof er sprake is van onafhankelijke vraag.
- Er wordt gekeken naar het moment van bestellen en de te bestellen hoeveelheid, maar niet naar het moment dat het artikel nodig is.
- Alle voorraadpunten worden onafhankelijk van elkaar beoordeeld. Het voorraadbeheer wordt niet over de gehele keten geoptimaliseerd.
Productketenbenadering en JIT
Met de introductie van het MRP II-concept wordt een oplossing verstrekt voor de voornoemde problemen. We maken als eerste een onderscheid tussen de onafhankelijke (stochastische) vraag en de daaruit volgende afhankelijke (deterministische) vraag. Het hoofdproductieplan (HPP of MPS) is het punt waar de onafhankelijke stochastische vraag wordt omgezet naar de afhankelijke deterministische vraag. Vervolgens wordt op basis van het MRP I-concept de afhankelijke vraag afgezet tegen de geprojecteerde voorraadhoogten en indien noodzakelijk worden bestelhoeveelheid en bestelmoment middels het algoritme bepaald. Het is niet geheel toevallig dat het denken in het klantenorderontkoppelpunt (KOOP) in dezelfde tijd tot stand is gekomen. In het KOOP-concept komt het punt waarbij de ontkoppelvoorraad wordt gelegd, idealiter overeen met het MPS.
Ook al is het MRP-denken een welkome aanvulling op het klassieke voorraaddenken, het concept blijft het aanhouden van voorraad zien als enige reactie op de fluctuaties in het afnamepatroon. Omdat voorraad houden geld kost, zijn er als reactie op het MRP-denken andere zienswijzen ontstaan. In deze zienswijzen wordt het moeten aanhouden van voorraad vanuit andere invalshoeken bekeken. Zo zijn de Japanners de mening toegedaan dat voorraad de problemen bedekt. Om efficiënt te produceren is voorraad eigenlijk niet nodig. Het streven naar 'nulvoorraad' is één van de belangrijkste pijlers in de Just in Time-filosofie. De bedoeling hierachter is om levering en productie zodanig op elkaar af te stemmen dat er nauwelijks tot geen voorraden in een bedrijf nodig zijn. De leveringen gebeuren precies op tijd, dus er hoeft niets te worden opgeslagen. Dit zorgt uiteindelijk voor het wegvallen van de voorraadkosten en alle andere daarbij optredende kosten. Een groot nadeel is dat de minste verstoring in de toeleveringen de hele bevoorradingsketen plat kan leggen. Er zijn immers geen buffervoorraden meer.
De JIT-filosofie is echter meer dan alleen een logistiek concept. Het kent door bijvoorbeeld de zero defects-filosofie een sterke verwevenheid met het kwaliteitsdenken. Het proces lijkt dus erg op een lopende band, waarbij de productieprocessen (van verschillende bedrijven) naadloos op elkaar aansluiten. Deze zienswijze komt, net als MRP, tegemoet aan de bezwaren die kleven aan de klassieke voorraadtheorie. Het is overigens leuk om op te merken dat de door de Just in Time-theorie bekend geworden 'KANBAN' niet meer is dan een praktische vertaling van het BQ-systeem uit de klassieke voorraadtheorie.
De knelpuntbenadering
Helaas blijkt het geheel elimineren van voorraden tot nu toe een utopie. Goldratt heeft daarom een systeem bedacht dat weer een andere invalshoek kent. Hij maakt een onderscheid tussen knelpunten en niet-knelpunten. De knelpunten stellen hem in staat om de productie beter te sturen. Voor wat betreft de voorraad is hij in zijn filosofie erg duidelijk. Voorraad is niet wenselijk, maar helaas ook onvermijdelijk. Zijn definitie van voorraad wijkt daarom sterk af van de gangbare definities.
Voorraad is al het geld dat het systeem investeert in de aankoop van dingen die het systeem wil verkopen.
In zijn optiek is voorraad noodzakelijk om met behulp van het systeem geld te genereren. Op deze wijze brengt hij het traditionele voorraaddenken en het nulvoorraaddenken bij elkaar. In zijn Theory of Constraints (TOC) gaat hij uitgebreid in op de functie van voorraad.
Quick Response Manufacturing en Polca
Rajan Suri positioneert Polca als een van de tools voor het realiseren van Quick Response Manufacturing (QRM). Bij deze managementfilosofie staat doorlooptijdverkorting en daarmee kostenverlaging centraal.
Polca
Ten eerste wordt de werkvloer opgesplitst in productiecellen. Binnen zo'n cel voeren mensen en machines een bepaalde klasse van bewerkingen uit. In tegenstelling tot 'gewone' Lean Manufacturing is er geen sprake van een vaste route die de orders afleggen. Integendeel, de verschillende halffabrikaten bewegen zich kriskras over de werkvloer, waar ze – afhankelijk van het gewenste type eindproduct– productiecellen naar keuze aandoen. Vervolgens wordt het Polca-systeem ingevoerd. Alle productiecellen die materialen met elkaar kunnen uitwisselen, worden daarbij paarsgewijs verbonden via circulerende Polca-kaarten.
Op zo'n Polca-kaart staan aan de ene kant de gegevens van een toeleverende productiecel (T) en aan de andere kant de gegevens van een ontvangende productiecel (O). De clou is nu dat cel T alleen aan een product mag gaan werken dat door moet naar cel O als cel T een Polca-kaart T/O in zijn bezit heeft. Als cel O klaar is met de vervolgbewerking, wordt de T/O-kaart teruggestuurd. Op cel T wordt dan bekend dat er capaciteit op cel O is vrijgekomen, zodat de toelevercyclus van T naar O zich kan herhalen.
Het Polca-systeem lijkt een beetje op de toeritdosering van een snelweg. Door alleen productieorders toe te laten waarvoor er ruimte is verderop, wordt het ontstaan van files voorkomen. Is er nog geen capaciteit beschikbaar op een ontvangende productiecel, dan wordt er gewerkt aan orders die bij de verdere verwerking een andere route volgen. In hoofdlijnen lijkt QRM ook veel op de Theory of Constraints van Goldratt. De verschillen zitten hem in de details van aansturen. Volgens Suri zelf is de theorie van Goldratt meer geschikt in een situatie met een repetitief karakter en werkt QRM beter in een situatie waarin ieder product weer anders is.
Ondernemingsbenadering
Omdat de capaciteiten van computers en de verschillende programmeertalen tot voor de jaren tachtig te beperkt bleven, bleef het beeld van een enkel geïntegreerd informatiesysteem voor de gehele organisatie jarenlang een utopie. In plaats daarvan ontwikkelden ondernemingen voor elke functionaliteit een afzonderlijk informatiesysteem. Vaak waren de verschillende systemen amper met elkaar geïntegreerd. Hoewel MRP II een significante verbetering betekende ten opzichte van de vorige systemen, bleef als gevolg van de dynamische ontwikkelingen bij de ondernemingen de vraag bestaan naar meer geïntegreerde systemen. De nieuwe generatie van informatiesystemen moest dus sneller informatie beschikbaar kunnen stellen en ondernemingen als SAP, Oracle, PeopleSoft en Baan speelden daar perfect op in. Zo werd het Enterprise Resource Planning-systeem (ERP) ontwikkeld. De term 'ERP' werd geïntroduceerd door The Gartner Group in het begin van de jaren negentig. Terwijl MRP II zich traditioneel focuste op de planning van de interne middelen van de onderneming, streeft ERP ernaar ook de middelen van de leveranciers te plannen, gebaseerd op de dynamische vraag van de klanten. De introductie van ERP-systemen zou moeten leiden tot een betere doorstroming van bedrijfsprocessen, waardoor er minder afstemmingsverliezen ontstaan. Hierdoor kan de voorraad worden verminderd en daarmee kunnen de kosten worden teruggebracht.
Ketenbeheersing
Door de opkomst van informatietechnologie kon de reactiesnelheid van ondernemingen toenemen. Naarmate de beheersing in huis beter verliep, kwam de gedachte op om de gehele keten te gaan beheersen. Belangrijk doel was het terugdringen van voorraad en het beter afstemmen van vraag en aanbod. Het ERP-denken ging langzaam over in supply chain-denken. Forecasting maakte plaats voor Demand Management: kunnen we de vraag niet goed voorspellen, dan moeten we de vraag maar meer sturen. Daarnaast nam het gebruik van Point of Sale-informatie (PoS) sterk toe. Mede mogelijk gemaakt door de technologie van scanning en barcodering moest de keten al reageren op het moment dat uw boodschappen de kassa passeerden. De distributieketen werd de bottleneck in de keten. Waarom eerst goederen in een centraal magazijn op voorraad leggen, terwijl ze ook rechtstreeks overgeslagen konden worden in een andere vrachtwagen? Met name voor versgoederen heeft cross-docking een grote vlucht genomen. Als resultaat konden voorraden, met als bijeffect een betere informatiebetrouwbaarheid, zo nog verder geminimaliseerd worden. Doel van dit alles: een betere service tegen nog lagere kosten.
Voorbeeld Albert Heijn: Vandaag Voor Morgen
Albert Heijn heeft een nieuw distributiesysteem in gebruik genomen: Vandaag Voor Morgen (VVM). Het is een logistiek concept dat ervoor zorgt dat winkels binnen achttien uur hun levering krijgen. De winkels worden hierdoor vaker, sneller en op vaste tijden beleverd, waardoor ze hun bestellingen beter op de vraag van de klant kunnen afstemmen.
De vraag van de klant is bepalend voor wat er in de winkel wordt aangeboden, op welk moment en in welke hoeveelheden. De klant van vandaag is echter zeer wisselend in zijn wensen. Zijn gedrag verschilt van dag tot dag, van moment tot moment. Vandaag een kant-en-klare maaltijd, gemakkelijk en snel te bereiden. Morgen weer uitgebreid, compleet met wijn en nagerecht. Om ervoor te zorgen dat de klant kan rekenen op de juiste producten die op het juiste moment en op de juiste plaats worden aangeboden, is Albert Heijn overgestapt op een compleet nieuw logistiek concept: Vandaag Voor Morgen.
Vertrekpunt voor VVM is de scanningkassa. Daar wordt de actuele wens van de klant duidelijk. De scanningkassa legt die vast, vergaart de verkoopgegevens en zendt deze door zodat er een nieuwe bestelling kan worden opgemaakt. Met behulp van moderne informatietechnologie wordt deze bestelling doorgezet naar de verschillende distributiepunten en in toenemende mate direct naar de leveranciers. De gehele bestelling wordt na het moment van bestellen binnen achttien uur bij de winkel afgeleverd.
Door deze systematiek zijn hoogfrequente, snelle leveringen mogelijk. De rollen zijn daarmee in feite omgedraaid. Vroeger werden de winkels op grond van het voorspelbare consumentengedrag bevoorraad. Maar de tijd dat er op woensdag gehakt werd gegeten en op vrijdag vis ligt achter ons. De klant is onvoorspelbaar geworden. Binnen VVM bepaalt daarom de actuele vraag van de klant wat er de volgende dag bij de achterdeur van de winkel wordt afgeleverd. Het gaat er daarbij om de juiste hoeveelheid op het juiste moment aan te leveren. Niet te vroeg want dat leidt tot opslagproblemen en niet te laat want dat levert direct lege schappen op. Een bijkomend voordeel hiervan voor de winkels is dat magazijnruimte kan worden opgegeven ten gunste van verkoopoppervlak. De winkel kan zo een breder assortiment gaan voeren. Dure vierkante meters in winkelgebieden kunnen zo rendabeler worden ingezet. Als afgeleide van deze ontwikkeling neemt ook de gemiddelde voorraad binnen de logistieke keten af. De hoofdtaak van de distributiecentra verschuift van de voorraadfunctie naar de verdeelfunctie. Het houden van voorraden wordt stroomopwaarts in de logistieke keten gelegd.
Daarnaast wordt het verkooppatroon aan een aantal leveranciers direct doorgegeven. Ook deze 'co-maker' leveranciers kunnen zo optimaal inspringen op de klantvraag. Dit is een belangrijk uitgangspunt van VVM: de leveranciers worden direct op de totale logistieke keten aangesloten. Ook zij zullen in staat moeten zijn om van batchgeoriënteerde processen om te schakelen naar een flowproductie. Voor de co-maker leveranciers geldt dat zij met de door de AH-vestigingen verstrekte scanningkassagegevens hun eigen productie kunnen afstemmen op de klantvraag. Ook bij de leveranciers kan onnodige voorraadvorming op deze wijze worden voorkomen.
Het aflevertijdstip wordt aan de winkels op vijftien minuten nauwkeurig aangegeven. Afhankelijk van de omzet en het aantal beschikbare meters in de vestiging wordt een tweede of eventueel derde levering per filiaal per dag vastgesteld. De vastgestelde afleveringen vinden gedurende de week altijd op dezelfde tijdstippen plaats; hierdoor wordt de aansturing van het logistieke proces een stuk eenduidiger. Door de hoogfrequente aanvoer blijven de hoeveelheden hanteerbaar, namelijk precies voldoende tot de volgende aflevering. De winkel kan snel worden gevuld zodat de medewerkers meer tijd aan de klant kunnen besteden.
Dit dossier is eerder verschenen bij WEKA Uitgeverij in Rendement met Kwaliteit. Auteur: Paul Denneman